Prepare for your California BIT inspection with key maintenance steps for a smooth process. Learn how to ensure fleet readiness and compliance.
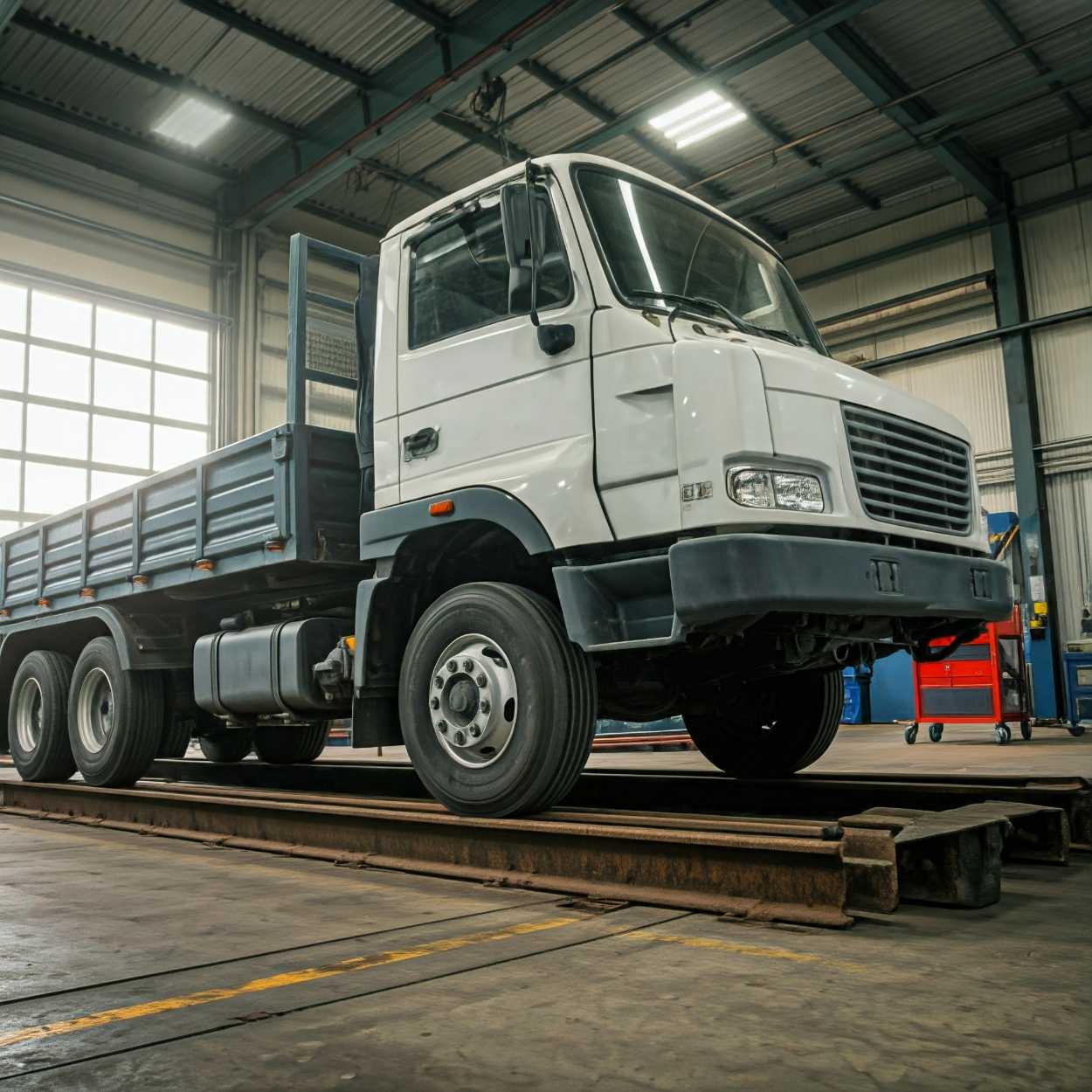
The Basic Inspection of Terminals (BIT) isn’t just a standard checkup for your fleet—it's a critical examination that can have significant implications for compliance and safety. Preparing your vehicles for a smooth BIT inspection in California involves a comprehensive plan that aligns with stringent state standards. For fleet managers and owners alike, a successful BIT inspection not only avoids fines but also ensures safe and dependable equipment on the road. Let’s break down the essentials of a BIT inspection and the steps you should take to breeze through it.
What is a BIT Inspection?
The BIT program, mandated by the California Highway Patrol (CHP), requires that certain commercial motor vehicles undergo inspection every 90 days to ensure safety and compliance. BIT inspections focus on various aspects of vehicle maintenance, record-keeping, and safety procedures. Areas inspected include, but are not limited to, brakes, tires, lights, and load security. Each inspection provides a snapshot of a fleet’s adherence to maintenance standards, so being prepared is a must.
Key Preparation Steps for BIT Inspection
1. Stay on Top of Maintenance Records
Maintenance records are the backbone of BIT compliance. This includes detailed records of regular and preventive maintenance for each vehicle in your fleet. An accurate maintenance log can save you time and ensure you don’t miss any requirements.
- Include Details: Each entry should specify the date of service, type of maintenance performed, and who completed it. Whether you handle these records manually or use a fleet management software, consistent, detailed entries are essential.
- Vehicle History: Log historical data on each vehicle’s repairs, replacements, and inspections to give inspectors a clear view of your maintenance practices.
2. Implement Routine Preventive Maintenance
Preventive maintenance can help you catch and address issues before they escalate, ensuring your fleet is always BIT-ready.
- Brake System Checks: Brakes are a high-priority item in any BIT inspection. Perform regular brake inspections to check for wear and tear, fluid leaks, and other issues. Pay attention to drum brakes and slack adjusters to ensure they function properly.
- Tire Inspections: Tires should have adequate tread depth and be free of sidewall cracks or uneven wear. Perform weekly checks to ensure all tires meet DOT tread depth requirements and are inflated to the correct PSI.
- Lighting Systems: Ensure that all lights are operational. This includes headlights, taillights, and reflectors, which are crucial for visibility and compliance.
- Suspension & Steering: Components like shock absorbers, leaf springs, and steering linkage should be inspected regularly for wear or damage that could impact vehicle stability.
3. Develop an Organized Inspection Process
A well-organized inspection process helps avoid delays and missed items on the BIT checklist. Create a checklist that covers each component the CHP will evaluate, and train your team to conduct mock inspections using this list.
- Checklist Components: Include brakes, tires, lights, steering, suspension, and cargo securement.
- Regular Mock Inspections: Conduct these “dress rehearsals” every month or so. Mock inspections can reveal potential compliance issues and allow time for any necessary repairs.
4. Train Your Drivers on Inspection Standards
Drivers play a critical role in the daily upkeep of your fleet and should be trained to recognize signs of wear or potential issues before they become major problems.
- Pre-Trip Inspections: California mandates daily pre-trip inspections, which should include checks on brakes, lights, tires, and general vehicle conditions. Drivers should be trained to note anything out of the ordinary and report it promptly.
- Reporting Protocols: Set up a system for drivers to log any defects or unusual performance in their vehicles. Consistent feedback from drivers helps keep vehicles BIT-compliant.
5. Keep Your Fleet Organized and Clean
Believe it or not, cleanliness and organization can impact your inspection results. A clean and orderly fleet demonstrates a commitment to maintenance and makes it easier to spot potential issues.
- Clear Out Clutter: Remove unnecessary items or trash from the cab and cargo area. A tidy workspace reflects positively during an inspection.
- Fleet Uniformity: If possible, organize your fleet so that all vehicles are in similar condition, with no apparent signs of neglect.
6. Ensure Accurate Documentation
Document control is essential for BIT compliance. Keeping up with logbooks, inspection sheets, and maintenance records is crucial in demonstrating compliance.
- Driver Logs: Ensure drivers accurately complete their logs, noting all stops, maintenance, and inspections.
- Inspection Reports: Maintain and file reports from all pre-trip, periodic, and BIT inspections. Keep them readily available in case of audits.
7. Stay Updated with Regulatory Changes
California’s BIT regulations are subject to change, and compliance depends on staying informed. Be sure to stay up-to-date on any new laws or alterations to inspection procedures.
- Periodic Review: Have a designated team member regularly review the latest CHP announcements on BIT inspections.
- Training Updates: As regulations evolve, provide ongoing training for staff to ensure they are familiar with any new standards.
Avoiding Common BIT Inspection Pitfalls
Even with thorough preparation, there are some common missteps that could lead to non-compliance during an inspection. Here are a few to watch out for:
- Inconsistent Records: Gaps in maintenance records can be a red flag. Ensure every repair and inspection is documented.
- Neglecting Tire Conditions: Worn or improperly inflated tires can lead to inspection failure. This is one area inspectors scrutinize closely.
- Ignoring Minor Issues: Small, seemingly insignificant issues like a broken reflector or a dim tail light can add up in an inspection report. Address minor repairs promptly to avoid them impacting your inspection results.
The Benefits of BIT Inspection Readiness
Being well-prepared for your BIT inspection has its advantages beyond regulatory compliance. A well-maintained fleet is safer, more efficient, and less likely to experience costly breakdowns. Adhering to BIT standards also protects your business from potential fines or other legal ramifications. By prioritizing these inspections, you contribute to a safer, more reliable industry standard, giving peace of mind to both your drivers and the public.
Final Thoughts
Preparing for a BIT inspection may seem challenging, but with a proactive approach and consistent maintenance, it becomes a straightforward process. By staying on top of preventive maintenance, keeping accurate records, and educating your team on BIT requirements, your fleet will be inspection-ready, safe, and efficient. Every detail matters in keeping your fleet on the road and BIT-compliant, and with these tips in place, you’re setting the stage for inspection success.
For expert help in getting your fleet BIT inspection-ready, A Plus Mobile Maintenance in Brea, CA is here to support you every step of the way. Reach out to us today to ensure your vehicles are safe, compliant, and ready for the road ahead!
Contact Us
Get in touch with A Plus Mobile Maintenance today for mobile truck repair and fleet services. We provide service to San Bernardino, Riverside County, Los Angeles County, Orange County, Anaheim, & more!