Discover the 7 most common lift gate problems and how to fix them. A Plus Mobile Maintenance in Brea, CA, offers expert repair and preventive maintenance services.
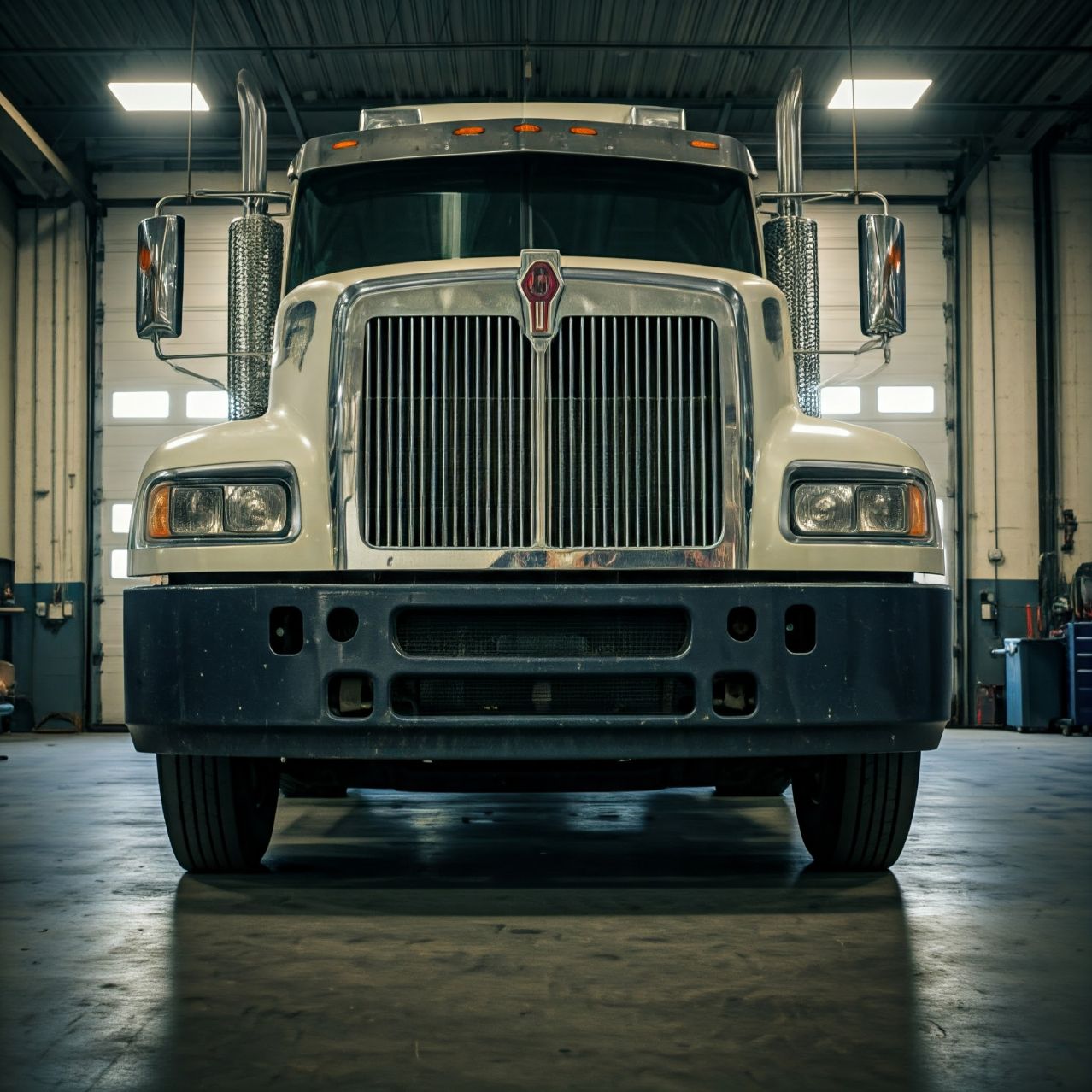
Lift gates are indispensable tools for commercial vehicles, simplifying the process of loading and unloading heavy cargo. However, these hardworking systems are prone to wear and tear, especially without proper maintenance. Whether you’re running a fleet or managing a single truck, recognizing and preventing lift gate issues can save you time, money, and a lot of frustration. Let’s dive into the seven most common problems and practical steps to avoid them.
1. Hydraulic Leaks
Hydraulic systems are the backbone of your lift gate, providing the power needed to raise and lower heavy loads. A leak in the system can render the lift gate inoperable.
Causes
- Worn-out hoses or seals.
- Improper connections or fittings.
How to Avoid It
- Inspect hydraulic hoses and seals regularly for signs of wear or damage.
- Tighten loose connections and replace compromised components promptly.
Pro Tip: Always use manufacturer-recommended hydraulic fluid to prevent internal damage.
2. Electrical Malfunctions
Electrical issues are a leading cause of lift gate failure. Problems with the wiring or control switch can prevent the gate from responding to commands.
Causes
- Corroded or frayed wires.
- Faulty control switches.
- Drained or insufficient battery power.
How to Avoid It
- Inspect and replace damaged wiring and connectors.
- Test the control switch regularly and keep a spare on hand.
- Ensure your battery is fully charged and capable of supporting the lift gate’s operation.
3. Lift Gate Won’t Raise or Lower
Few things are more frustrating than a lift gate that won’t move when you need it. This can be caused by several mechanical or electrical issues.
Causes
- Hydraulic fluid levels are too low.
- A jammed or damaged lifting mechanism.
- Electrical circuit failures.
How to Avoid It
- Maintain proper hydraulic fluid levels and inspect for leaks.
- Lubricate the lifting mechanism periodically to prevent jamming.
- Perform regular tests to ensure all components are functioning properly.
4. Uneven Platform Movement
An uneven platform can make loading and unloading dangerous, potentially damaging cargo or causing injury.
Causes
- Misaligned or damaged lift arms.
- Unequal hydraulic pressure distribution.
How to Avoid It
- Align the platform and adjust lift arms during routine maintenance.
- Ensure hydraulic cylinders and lines are balanced and functioning correctly.
Pro Tip: Train operators to load cargo evenly on the platform to reduce unnecessary strain.
5. Excessive Noise During Operation
Unusual noises, such as grinding or screeching, often indicate that something isn’t functioning as it should.
Causes
- Lack of lubrication on moving parts.
- Worn or damaged gears, bearings, or pins.
How to Avoid It
- Lubricate all moving parts regularly with manufacturer-recommended grease.
- Replace worn or damaged components before they fail completely.
6. Lift Gate Won’t Lock in Place
A lift gate that doesn’t lock can create a safety hazard and damage the gate or cargo during transit.
Causes
- Worn locking pins or latches.
- Misaligned locking mechanism.
How to Avoid It
- Inspect and replace locking pins and latches as they wear.
- Test the locking mechanism after every repair or adjustment to ensure alignment.
7. Overloading the Lift Gate
Overloading is one of the fastest ways to damage your lift gate. Exceeding the weight limit can stress hydraulic systems and compromise structural integrity.
Causes
- Ignoring the manufacturer’s weight limit.
- Unevenly distributed loads.
How to Avoid It
- Always adhere to the lift gate’s weight limit.
- Train operators to evenly distribute weight across the platform.
Best Practices for Preventing Lift Gate Problems
- Schedule Regular Maintenance: Routine checks can catch small issues before they become major problems.
- Clean the System: Dirt and debris can clog hydraulic and mechanical components, so clean the lift gate after heavy use.
- Train Operators: Proper use is critical. Train employees on weight limits, load distribution, and how to operate the gate safely.
- Keep Spare Parts on Hand: Common items like hydraulic fluid, control switches, and locking pins should always be available.
Conclusion
A properly maintained lift gate can save you countless hours of downtime and unexpected repair costs. By staying proactive with maintenance and addressing minor issues early, you’ll ensure your lift gate remains reliable and safe.
At A Plus Mobile Maintenance in Brea, CA, we specialize in lift gate inspections, repairs, and preventive maintenance. Contact us today to keep your lift gates operating smoothly!
Contact Us
Get in touch with A Plus Mobile Maintenance today for mobile truck repair and fleet services. We provide service to San Bernardino, Riverside County, Los Angeles County, Orange County, Anaheim, & more!